TRADITIONAL SHOEMAKING CRAFT FACING EXTINCTION
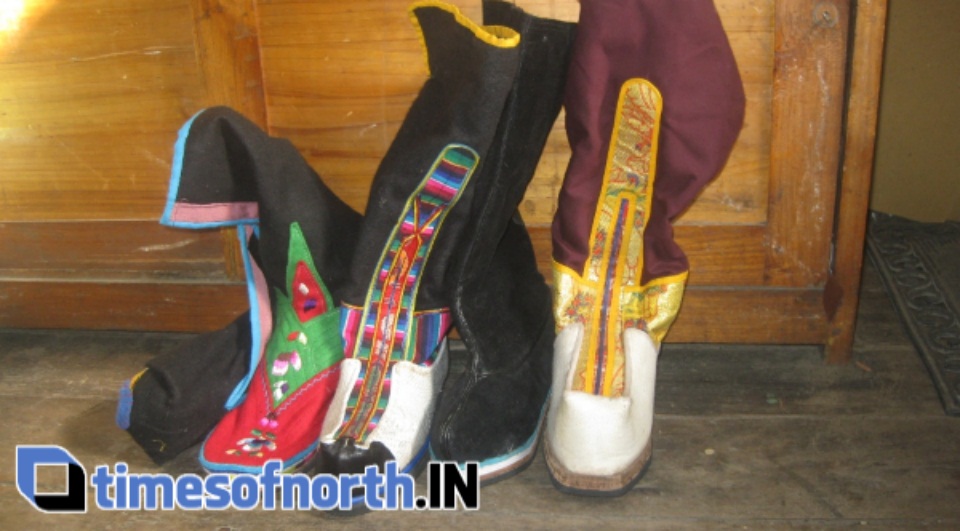
Nisha Chettri
The aesthetic interest along with the craftsmanship in designing embroidered shoes in Kalimpong is an endangering profession today. Wrestling with the evolution of modernity and the shrinkage of ethnicity, the shoemaker of Kalimpong breathe in anxiety and feels that the profession will no longer inherit to the next generation. Arjun Lama, a professional Tibetan shoe maker, of Wongmo Villa, Kalimpong, has been doing this since the last 34 years. Spending most of his life making these shoes, he learnt a lot about the culture, history and traditions of the craft. In a conversation he recalls the time he learnt the art of making traditional footwear from an old man from Tibet named as (late) Pasang Dorjay Bhutia, who was locally known as Pala. I was in my early twenties when I first learnt about shoes from Pala; I couldn’t study more, that’s how I decided to make traditional shoes’ said Lama, where he added that those shoes in Tibet once spoke about the status, gender, ethnicity, religion and profession of a person who wore them and also said that it was once worn only by the Tibetan aristocracy which gradually evolved to be a necessity of common people. The history of the footwear also talks about keeping them warm and protecting their feeble knees from cold, snowy weather of Tibet. The materials he works with in making footwear’s are leathers (oxhide/cowhide), jutes, fabric materials, wools, etc,. He explained that the shoes are made with the type of orders people make and the names of the traditional boots varies according to the status of people, ‘the type of boots Lama’s (monks) wear is known as Ration, which means rainbow in Chinese, it carries a religious meaning, ladies wear is known as Somba, boots worn by the average people is known as Ghalo and the types school Tibetan dancers wear is known as pumalam.’ It was known that the boot have no distinction between left and right, and is divided into different sections while making, each of which is later assembled into a full piece and the base part or sole is often made up of cowhide or buffalo hide. Lama also talks about the changes that accompanied the traditional design, he said, ‘the shoe is actually made for the ones who stay in snow and the sole made of cowhide are slippery there which is now alternated by a rubber sole.’ Revealing the destination of exports of his ethnic designs he said that his footwear’s are ordered from Bhutan, Nepal, Tibet (via Nepal) and Dharamshala (Himachal Pradesh) have ordered maximum number of boots till date. It was also known that many people have visited him from Kolkata, Jaipur and Ahmadabad to learn the craft of shoemaking. ‘I have trained a Bengali boy for a month, handful of Jaipuris and few people from Ahemdabad for some time’ informed Lama and said that no one from Sikkim or Darjeeling have approached him in order to learn the craft.
The entrepreneur now feels that the tradition is creating a void space and people glued in modernity epoch are embarrassed to take shoemaking as their profession, moreover he doesn’t want his offspring to carry the burden of the laborious inheritance, ‘My vision has already deteriorated because of this job; I don’t want my offspring’s to go through the intensity of hard work like I did’ said Lama. Adding to that he said that he is happy with his small shop and doesn’t want to upgrade it. However the range of his designed footwear starts from 2700 rupees till 5000 rupees and he manages to make two pairs of shoes in a day with his blurry vision and 100 pairs within a year which depends on the weather condition. Besides the Buddhist buyers (from Nepal, Bhutan and Tibet) the international voyagers or the foreigners buy Tibetan boots as a good tourism souvenir from Kalimpong (’s tour). Although less people choose to wear the traditional boots here, but as a form of ethnic handicraft, the Tibetans want to preserve it. Lama also talks about his love for shoemaking and also tells that he will keep making shoes till his last breath.
Pictures: Nisha Chettri (TNI)